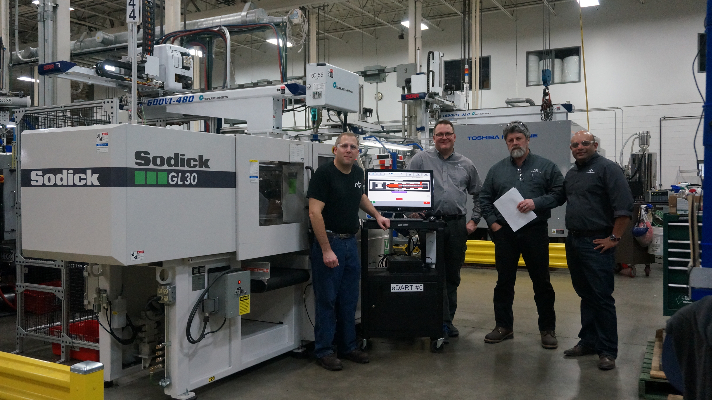
The Challenge
We have faced a few challenges, including short shot detection and segregation (in process and on start-ups/re-starts) and detecting irregular viscosity changes that cause quality issues. We also hoped to gain insight into what our process was producing during new product development and production through monitoring cavity pressure. In order to address these concerns, we tried cavity pressure monitoring through the use of PLCs as well as a competitor’s system. Both were not as comprehensive in their capabilities, too time consuming to implement, and too complex for production staff to embrace or maintain.
The Solution
We started using the eDART® System in 2011, then registered for RJG’s training shortly after that. The implementation was a major cultural paradigm shift for most of the team—it took the full support of the company to embrace the changes to the status quo. After some of the successes were recognized, the implementation process started flowing easier. Decisions and changes are no longer as challenging when you can back them up with data and understanding.
We chose RJG’s training courses because they are well recognized and respected in the industry, and they compliment our internal training very well. RJG training goes into greater depth than most, it’s challenging, and you get a sense of accomplishment when you complete a course. Our two companies working together sets us up for success.
The Result
We have since changed the way we run our processes. We develop and maintain them with a focus on the plastic’s point of view instead of machine settings. Rather than adjusting a process for an undesirable condition, we now identify the root cause of the change or issue and address that, considering all the components involved. We immediately noticed a significant descending trend of scrap and cost of quality as well as a reduction in troubleshooting time on properly launched products.
We increased our number of eDART Systems in 2017 by 25% and will likely exceed that in 2018. In-mold sensors are a standard part of our new tooling build and have been for a few years now. Also, the majority of our transfer work gets sensor implementation as well. Our customers and prospective customers have more confidence in our ability to support their needs since we can demonstrate that we operate within a controlled process.
Eric Pipkin
Technical Operations Manager
New Berlin Plastics
About New Berlin Plastics
New Berlin Plastics is a custom plastics injection molder that partners with OEMs and tiered suppliers that require high quality products, engineering services, and value-added activities from a single supplier. We strive to be a partner that handles projects from start to finish by leveraging our internal capabilities with those of other high-quality area companies.