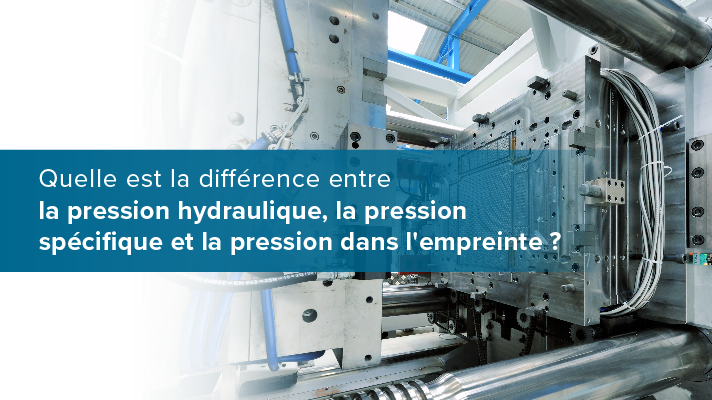
Toutes les pressions ne sont pas égales. Il y a différentes parties de la presse à injecter qui font l’objet de surveillance de pression et il est important d’examiner chacune individuellement pour mieux comprendre ce qui se passe avec le plastique à l’intérieur du moule.
Passons en revue les trois types de pression exercées dans la machine (hydraulique, spécifique et empreinte) et ce qui les différencie (rapport d’intensification et perte de charge).
Les types de pression
La pression hydraulique : il s’agit de la pression dans le vérin d’injection, générée par la résistance à l’écoulement de l’huile délivrée par une pompe hydraulique.
La pression spécifique : également appelée pression d’injection ou pression plastique, il s’agit de la pression réelle du matériau à l’intérieur de l’ensemble vis-fourreau générée par une résistance à l’écoulement du plastique devant la vis pendant l’injection. En règle générale, les presses à injecter hydrauliques affichent la pression d’huile hydraulique. Certaines afficheront également une pression spécifique. Les presses à injecter servo-électriques affichent une pression d’injection spécifique, pas la pression d’huile hydraulique.
Il est important de connaître la pression spécifique, car elle vous permet de documenter la pression d’injection et de sélectionner une machine adaptée.
La pression empreinte : il s’agit de la pression réelle du matériau à l’intérieur des cavités du moule elles-mêmes. Pour la mesurer, le moule doit être équipé de capteurs de pression.
Quelle est donc la différence entre ces différentes pressions ? La pression ne devrait-elle pas être la même partout ? Pas du tout !
Si vous observez un système de contrôle de process (tel que), vous vous apercevrez que les mesures entre ces trois types de pression varient considérablement. Cela est dû au rapport d’intensification et aux pertes de pression.
Le rapport d’intensification
Le rapport d’intensificationest le rapport entre la surface du cylindre d’injection et la surface de l’ensemble de pointe de vis. Le cylindre d’injection sera toujours plus grand et l’ensemble de la pointe de la vis sera toujours plus petit, ce qui induit une intensification de la pression.
A titre d’illustration, pensez à quelqu’un qui utilise une planche à découper pour enfoncer un clou au lieu d’utiliser un marteau. A force égale, le marteau va transférer plus de pression car l’énergie est moins diffuse du fait d’une surface de contact plus faible.
Chaque machine a un rapport d’intensification. Il est important de connaître ce ratio avant de régler le process. La détermination du ratio d’intensification se fait à l’aide d’une formule simple :
La perte de pression
La perte de pression se produit lorsque vous (vous l’aurez deviné) perdez de la pression lors du remplissage d’une pièce. La pression commence à diminuer à l’instant où elle sort de la buse.
Lorsque le plastique sort de la buse, sa pression est nettement plus élevée que lorsqu’il atteint le seuil. La perte de pression se fait en passant la pointe de la buse, la carotte, le système de canaux et le seuil. Plus vous vous éloignez du fourreau, plus la pression est faible. Comme vous pouvez l’imaginer, la pression dans la cavité est nettement inférieure à la pression hydraulique.
Conclusion
En tenant compte des pressions hydrauliques, des pressions spécifiques et des pressions d’empreinte ainsi que du rapport d’intensification et des pertes de pression, vous pouvez obtenir une image assez claire de ce qui arrive au plastique lorsqu’il se déplace dans la presse à injecter.