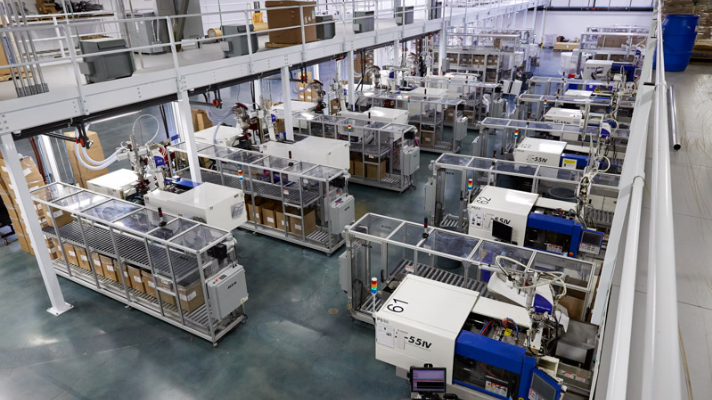
The Challenge
Before working with RJG, our process was largely trial and error, but we are always looking for a way to improve. When we were approached by a customer that required large amounts of SPC data and CPK studies for some of their more vital parts, we needed to find a way to meet these requirements without increasing the amount of labor.
We also had a high-volume critical part that we had been producing for many years that would periodically start to blister for reasons that we could never understand. We had the resin supplier analyze our process on multiple occasions, and they could never correct the problem. They felt our process was perfect. Our first engagement with RJG involved this part. The problem was corrected immediately, and we made a company-wide commitment to RJG at that moment and have never looked back.
The Solution
We learned about RJG’s products and trainings through our partnership with the MAPP organization and began working with them in 2009. The implementation of RJG technology across the full PCI platform occurred over several years, with the full support of the entire RJG organization.
We have hard-wired eDART® Systems on EVERY new press that we have brought into our facilities over the past 7 years (approximately 35 presses). We have retro-fitted all other presses, so all 61 presses in both PCI facilities are fully RJG compatible. We have also added RJG sensors to EVERY mold we have built over the past 7 years (approximately 350 molds).
To further leverage the technology, PCI contracts RJG’s Consultant/Trainers multiple times a year. They are very knowledgeable about their equipment and molding processes in general. These trainings help us discover new ways to successfully use RJG to improve production for us and our customers.
The Result
RJG has provided us with both quality gains and cost savings. In using the software, we are able to lower the frequency of quality checks needed to ensure good parts. Using the eDART System and in-mold sensors is like having a full-time auditor at each press.
The eDART System automatically stores all of the data from each run. We can use this data to assure our customers that we are making them quality parts with every shot and rejecting anything that does not meet the quality standards. RJG provides our customers with confidence that their products will be produced consistently from part one to part 2,000,000 and beyond, from January 1st to December 31st each year.
Chris Laverty
Manufacturing Engineer
Plastic Components, Inc.
About Plastic Components, Inc.
Plastic Components, Inc. was founded in 1989 in a 10,000 square foot facility with three molding presses and a vague concept of a plan to build a “fully-automated” manufacturing facility. Now, we have grown to two fully automated facilities, totaling over 78,000 square feet. We ship over 25,000,000 parts a month to the small engine, water faucet, and consumer goods industries all over the world.