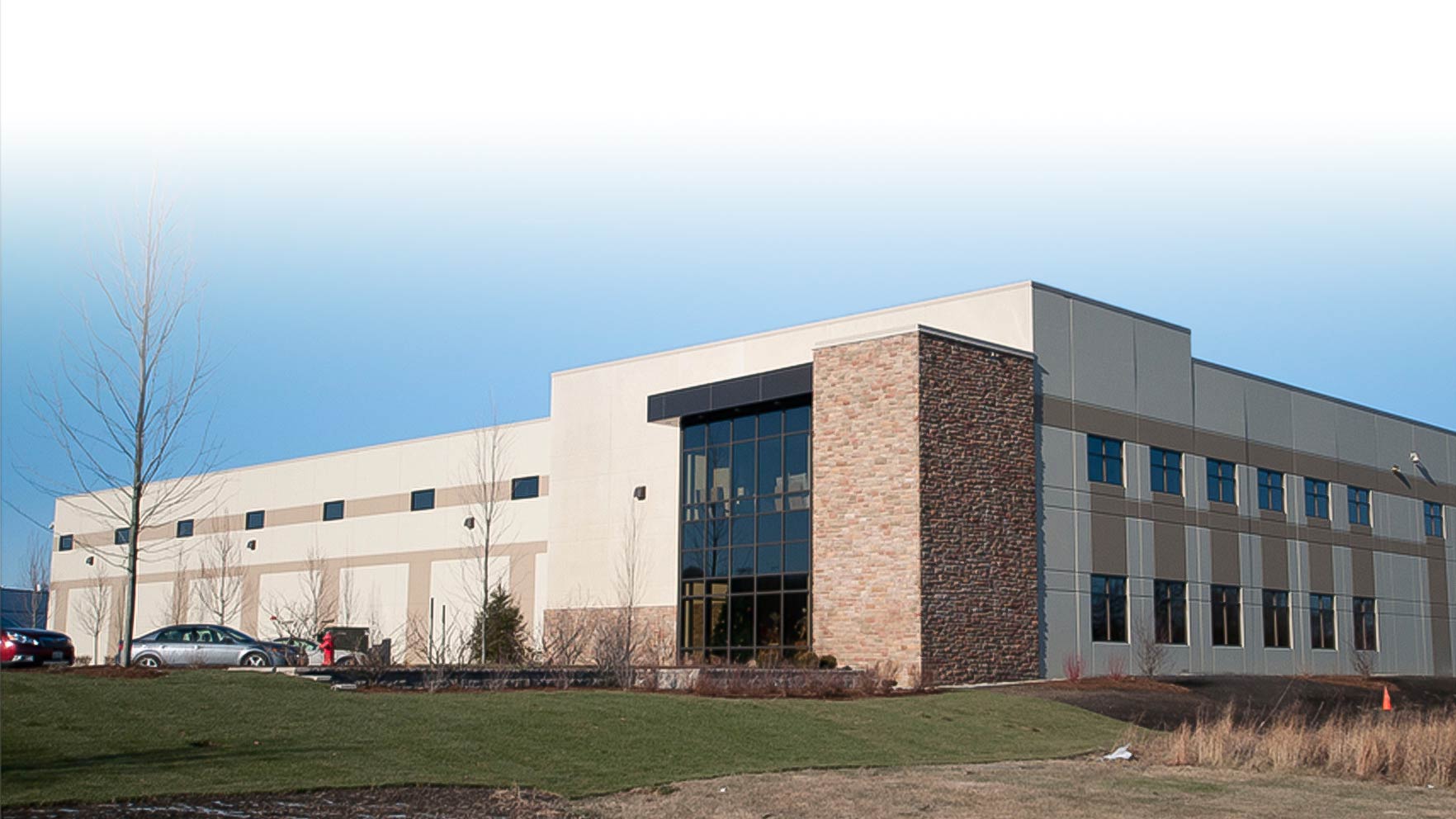
The Challenge
Our biggest challenge was product quality and verification. We run a high cavitation, fast cycle with critical dimensional requirements for this medical product. We produce millions of parts in a very short period of time.
This means if there is a quality concern, we would have to recall millions of parts from an offshore distribution location. The monetary and credibility cost of a recall this size in the medical industry is enormous, so it’s vital that we know every part that leaves the plant exceeds the customer’s quality expectations. Prior to RJG, this was a huge concern, and other techniques we tried to address it were unsatisfactory.
The Solution
We were familiar with RJG through past experience, so RJG was an obvious solution for us. The implementation was extremely smooth—RJG played a significant role in assistance from start to finished process. Their consultants were available whenever we had a question and were more than happy to help.
After installing RJG equipment, our staff attended RJG training. Since we were already working with RJG, we eased into training seamlessly, and they were able to gear it directly to our needs.
The Result
Within the first day of implementation, we could see the impact of RJG’s technology. We have greatly improved the quality of our products and can now document and validate the results with confidence. Having this data allows us to provide accurate information to our customers and be proactive in many aspects that, under normal procedures, would have been based on assumptions.
Our customers have a clear understanding of what RJG allows us to see, understand, and document, which clearly provides them with a higher level of confidence that their product is the best it can be. After such a successful implementation, I see only positive reasons why we would use other RJG equipment in the future.
Fred Chamberlain
VP Operations
Dana Molded Products
About Dana Molded Products
Dana Molded is a family-owned, custom injection and blow molder established in 1965 and ISO 9001 since 2003. Our long-term, dedicated staff has one goal: to provide solutions for customers. In 2011, we moved into a new, 90,000 square foot facility. Dana utilizes 32 injection molding machines from 20-610 tons, 8 blow molding machines, in-mold labeling, robotics, assembly, in-house engineering, product design, and a tool room with support of full time QA departments.